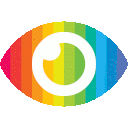
1. Electrostatic powder spreading (ESPS) is a method for depositing powder layers without mechanical contact with previous layers, allowing for the incorporation of multiple materials onto each layer in powder bed additive manufacturing processes.
2. ESPS uses an electric field formed between a powder container and a counter electrode to move powder particles from the container to the powder bed, with the rate of deposition controlled by adjusting the strength of the electric field.
3. ESPS represents a method to produce an arbitrary patterned multi-material powder bed without complicated powder removal steps and easy implementation into existing L-PBF machines, presenting an opportunity to build parts with 3D gradients in material properties.
The article titled "Electrostatic powder spreading for metal powder bed fusion applications" presents a new technique for depositing and patterning metal powders in additive manufacturing processes. The authors demonstrate the feasibility of electrostatic powder spreading (ESPS) for laser powder bed fusion (L-PBF) by building nearly fully dense coupons using the ESPS setup. They also achieve 2D patterning of a single layer by using an array of electrodes and switching the applied electric field on and off.
The article provides a detailed explanation of the theory behind ESPS, including the electrophoretic motion of particles and the critical electric field strength needed for particles to move in an electric field. The authors also describe their experimental methods, including measuring mass deposition rates and powder layer height.
Overall, the article appears to be well-researched and informative. However, there are some potential biases and missing points of consideration that should be noted.
One potential bias is that the article focuses solely on the benefits of ESPS without discussing any possible drawbacks or limitations. For example, it is not clear how ESPS compares to other techniques for depositing multiple powders on a single layer or whether there are any risks associated with using this method.
Additionally, while the authors provide a detailed explanation of the theory behind ESPS, they do not provide much information about how this technique could be implemented in practice. For example, it is not clear how difficult it would be to incorporate ESPS into existing L-PBF machines or what kind of training would be required to use this method effectively.
Another potential limitation is that the authors only demonstrate 2D patterning of a single layer using an array of electrodes. It is unclear whether this technique could be used to create more complex patterns or gradients in material properties in three dimensions.
Despite these limitations, the article provides valuable insights into a new technique for depositing and patterning metal powders in additive manufacturing processes. With further research and development, ESPS could potentially revolutionize the way that multi-material parts are fabricated using L-PBF and other powder bed fusion techniques.