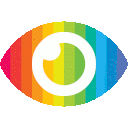
1. A novel method for preparing shape-stabilized composite phase change materials (SSPCMs) was presented using photosensitive resin and polyethylene glycol via UV curing.
2. The thermal and mechanical performance of the samples composited by the proposed method were measured, with the sample showing good capacity for phase change heat storage.
3. The effects on the sample's mechanical performance have been discussed in detail, with the optimal monolayer exposure time being 13.5 s and the monolayer curing depth being 40 µm for the sample with a 50% resin mass fraction.
The article titled "Additive manufacturing of shape-stabilized composite phase change materials via ultraviolet curing" presents a novel method for preparing shape-stabilized composite phase change materials (SSPCMs) using photosensitive resin and polyethylene glycol (PEG) via UV curing. The article provides a detailed description of the preparation process, including the raw materials used, light-cured reaction, material preparation, and characterization techniques.
The article highlights the advantages of SSPCMs over traditional solid-liquid PCM in terms of stability and mechanical strength. The authors also discuss the various methods used to prepare SSPCMs and compare them with their proposed method. They claim that their method is simple, efficient, and produces samples with good thermal and mechanical properties.
However, the article has some potential biases and limitations that need to be considered. Firstly, the study only focuses on one type of PCM (PEG), which may limit its generalizability to other types of PCMs. Secondly, the study does not provide any information on the environmental impact or potential risks associated with using photosensitive resin or UV curing.
Additionally, while the authors claim that their method produces samples with good thermal and mechanical properties, they do not provide any comparative data with other methods or materials. This lack of comparison makes it difficult to assess whether their method is truly superior to others.
Furthermore, the article does not explore any potential counterarguments or limitations of their proposed method. For example, it is unclear how well this method would work for larger-scale production or if there are any limitations in terms of sample size or complexity.
Overall, while the article presents an interesting new approach for preparing SSPCMs using 3D printing technology, it has some limitations in terms of generalizability and lack of comparative data. Further research is needed to fully evaluate the effectiveness and potential risks associated with this method.