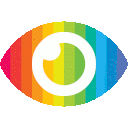
1. Researchers have achieved 3D printing of infrared transparent ceramics for the first time using material extrusion (MEX) technology.
2. The team developed an aqueous ceramic ink with high solid content and excellent shear-thinning properties suitable for MEX, resulting in a hemispherical dome cover and flat disc being successfully printed.
3. After de-binding and two-step sintering processes, the ceramic component achieved a relative density of 99.85% and >70% infrared transmittance in the mid-infrared region (3-5 µm).
The article titled "3D printing of infrared transparent ceramics via material extrusion" discusses the fabrication of 3D printed infrared transparent ceramics using material extrusion. The article highlights the advantages of 3D printing in creating complex geometric structures that are not possible with traditional ceramic molding processes. The authors report that they have successfully fabricated a hemispherical dome cover and a flat disc using an aqueous ceramic ink with high solid content and excellent shear-thinning properties.
The article provides detailed information on the materials and methods used in the study, including the preparation of the ceramic ink, 3D printing process, and sintering processing. The authors also discuss the properties of 3Y-TZP (3 mol% yttria-stabilized tetragonal zirconia) ceramics, which exhibit superior transmittance in the range of 3-5 µm compared to other IR transparent ceramics such as spinel and Y2O3.
While the article provides valuable insights into the potential applications of 3D printed infrared transparent ceramics, there are some limitations to consider. Firstly, the study only focuses on one type of ceramic material (3Y-TZP), which may limit its generalizability to other types of ceramics. Secondly, while the authors report high relative density and transparency for their fabricated components, they do not provide any data on their mechanical strength or durability under different environmental conditions.
Additionally, there is no discussion on potential risks associated with using 3D printed infrared transparent ceramics in real-world applications. For example, it is unclear whether these materials are safe for use in high-pressure or high-temperature environments or if they pose any health risks due to their composition.
Overall, while this study provides valuable insights into the potential applications of 3D printed infrared transparent ceramics, further research is needed to fully understand their properties and limitations before they can be used in practical applications.