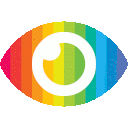
1. A low transition temperature steel (LTT) approach was used to develop carbon-martensitic hardenable hot work tool steel that can be processed to defect-free components by laser powder bed fusion (L-PBF).
2. A modified Schaeffler diagram was used to find an appropriate alloy composition as a starting point for alloy development, which was adapted to the L-PBF process by laser-remelting the surfaces of cast specimens with different Ni- and Cr-equivalents.
3. The commercially available alloy X38CrMo7–2 was adapted that can be processed using L-PBF without preheating of the build platform, and its microstructure and properties were compared with frequently used tool steel X40CrMoV5–1 (L-PBF-processed with preheating of the build platform of 300 °C).
The article presents a new approach for developing carbon-martensitic hardenable hot work tool steel that can be processed to defect-free components by laser powder bed fusion (L-PBF). The approach is based on low transition temperature steels (LTT), which are characterized by a low martensite start temperature at which the austenite transforms into martensite. The article describes the use of a modified Schaeffler diagram to find an appropriate alloy composition as a starting point for alloy development. The diagram was adapted to the L-PBF process by laser-remelting the surfaces of cast specimens with different Ni- and Cr-equivalents.
The article provides detailed information about the experimental procedures used to determine the retained austenite content and residual stress state of remelted surfaces, as well as the microstructure and properties associated with L-PBF-processed and heat-treated steel X38CrMo7–2. However, there are some potential biases in the article that need to be considered.
One-sided reporting: The article focuses solely on the development of carbon-martensitic hardenable hot work tool steel for L-PBF processing without preheating or specially adapted exposure strategies. While this is an important area of research, it would have been useful to provide more context about other approaches being used in industry and academia.
Unsupported claims: The article claims that no commonly used carbon-martensitic hot work tool steels can be L-PBF-processed without preheating of the build platform. However, this claim is not supported by any evidence or references.
Missing points of consideration: The article does not discuss any potential risks associated with using LTT steels for hot work tool applications. For example, it is possible that these steels may have reduced toughness or wear resistance compared to traditional hot work tool steels.
Missing evidence for claims made: While the article provides detailed information about the experimental procedures used to develop and test new alloys, there is limited discussion about how these alloys compare to existing materials in terms of their mechanical properties, cost-effectiveness, and ease of manufacturing.
Unexplored counterarguments: The article does not explore any potential counterarguments against using LTT steels for hot work tool applications. For example, it is possible that these steels may have reduced thermal conductivity compared to traditional hot work tool steels, which could impact their performance in certain applications.
Promotional content: The article focuses heavily on promoting the use of LTT steels for hot work tool applications without providing a balanced discussion of their advantages and disadvantages compared to other materials.
Partiality: The article only considers one commercially available alloy (X38CrMo7–2) for evaluation purposes, which limits its generalizability to other materials and applications.
In conclusion, while the article provides valuable insights into a new approach for developing carbon-martensitic hardenable hot work tool steel for L-PBF processing without preheating or specially adapted exposure strategies, it has some potential biases that need to be considered when interpreting its findings. Future research should aim to provide a more balanced discussion of different approaches being used in industry and academia and consider potential risks associated with using LTT steels for hot work tool applications.