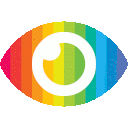
1. Researchers have developed a microscale multi-metal additive manufacturing technique called electrohydrodynamic redox printing (EHD-RP) that enables the direct printing and mixing of multiple, high-quality metals from a single nozzle.
2. EHD-RP combines the high spatial resolution of electrohydrodynamic (EHD) printing with the in situ generation and deposition of metal ions from sacrificial anodes, allowing for unmatched control of the 3D chemical architecture of printed structures and tuning of local properties through local alloying at the submicron scale.
3. The technique offers functional as-deposited materials properties without the need for additional processing, and allows for tailored local properties via tailored local chemistry, extending the classic approach of tuning properties by alloying to individual portions of a printed structure.
The article "Multi-metal electrohydrodynamic redox 3D printing at the submicron scale" published in Nature Communications introduces a new microscale multi-metal additive manufacturing (AM) technique called electrohydrodynamic redox printing (EHD-RP). The authors claim that EHD-RP overcomes the limitations of small-scale multi-material AM for metals, as it enables the direct printing and mixing of multiple high-quality metals from a single nozzle. The article highlights the potential of EHD-RP to additively manufacture batteries, thermocouples, bi-material metamaterials, and materials with locally tailored electrical resistance, chemical reactivity or microstructures.
The article provides detailed information on the working principle of EHD-RP and its advantages over existing AM concepts. It also presents results demonstrating the simultaneous printing of multiple metals from a single multichannel nozzle, on-the-fly variation of printed chemistry, high spatio-chemical resolution, nanocrystalline and dense microstructure, and tailored local properties via tailored local chemistry.
However, the article has some limitations. Firstly, it does not provide any information on the cost-effectiveness of EHD-RP compared to other AM techniques. Secondly, it does not discuss any potential risks associated with using EHD-RP for additive manufacturing. Thirdly, it does not explore any counterarguments or alternative perspectives on the use of EHD-RP for additive manufacturing.
In conclusion, while the article provides valuable insights into a new microscale multi-metal additive manufacturing technique called electrohydrodynamic redox printing (EHD-RP), it has some limitations in terms of discussing cost-effectiveness and potential risks associated with using this technique. Further research is needed to fully understand the potential benefits and drawbacks of using EHD-RP for additive manufacturing.