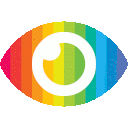
1. The article describes the development of a fluid-sealed direct shear apparatus capable of deforming large rock samples and monitoring fault-related fluid flow to large displacements.
2. The apparatus allows for absolute displacements up to 120 mm, which is nearly an order of magnitude higher than previous models.
3. The equipment is particularly suited for studying the continuity of clay smears and can be used to investigate the coupling of fluid flow and faulting during fault zone evolution.
The article titled "Design, operation and validation of a new fluid-sealed direct shear apparatus capable of monitoring fault-related fluid flow to large displacements" discusses the development of a new direct shear apparatus that allows for the deformation of large rock samples under fluid-sealed conditions. The authors highlight that existing testing configurations have limitations in capturing both mechanical and hydrological data during deformation, especially at elevated stresses and large strains. They argue that their new apparatus overcomes these limitations by allowing for larger displacements (up to 120 mm) and the study of hydromechanical coupling in intact rock samples.
One potential bias in this article is the focus on promoting the capabilities and advantages of the new apparatus without discussing its limitations or potential drawbacks. While the authors briefly mention some challenges related to maintaining a fluid seal during deformation, they do not provide a comprehensive analysis of these challenges or any potential issues that may arise when using their apparatus. This lack of discussion on limitations could be seen as promotional content aimed at highlighting the novelty and uniqueness of their equipment.
Additionally, the article does not provide a balanced view by presenting alternative testing configurations or approaches that may also be suitable for studying fault-related fluid flow. The authors only briefly mention other testing devices such as conventional triaxial rigs and ring shear devices but do not discuss their advantages or disadvantages in comparison to their own apparatus. This one-sided reporting limits the reader's understanding of the broader context and available options for studying fault-related fluid flow.
Furthermore, while the authors mention that finite element modeling was conducted to investigate the effects of cell geometry on stress distribution, they do not provide any details or results from these simulations. This lack of evidence for their claims about stress distribution in the sample undermines the credibility of their findings.
Another missing point in this article is a discussion on potential risks or limitations associated with studying fault-related fluid flow using large displacements. The authors focus primarily on the technical aspects of their apparatus and its capabilities but do not address any potential risks or challenges that may arise when deforming rocks to such large displacements. This omission leaves the reader without a complete understanding of the potential implications or limitations of their research.
In conclusion, while the article provides some valuable insights into the development of a new fluid-sealed direct shear apparatus for studying fault-related fluid flow, it has several biases and shortcomings. The authors' focus on promoting their equipment without discussing its limitations, lack of balanced reporting on alternative testing configurations, missing evidence for their claims, and failure to address potential risks or limitations all contribute to a biased and incomplete analysis.