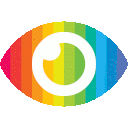
1. Rolls-Royce engineers are using a “smart customer” approach to work with the supply chain for cast parts, relying on ESI’s casting simulation software ProCAST.
2. The co-design workflow embedded in ProCAST enables them to be more proactive and identify most manufacturability issues before the part design is sent to the supplier.
3. Rolls-Royce engineers also routinely perform a cooling simulation they call “Magic Fill” which quickly predicts the parts properties after the cooling of the molten alloy.
The article provides an overview of how Rolls Royce verifies their cast parts, focusing on their use of ESI's casting simulation software ProCAST and their "smart customer" approach to working with suppliers. The article is written from a promotional perspective, as it focuses on how Rolls Royce is using this technology and does not provide any counterarguments or alternative perspectives. Additionally, there is no evidence provided for any of the claims made in the article, such as that 97% of potential casting issues can be located with this technology or that it can predict part properties after cooling of molten alloy. Furthermore, there is no discussion of potential risks associated with this technology or its use by Rolls Royce, nor does it present both sides equally in terms of advantages and disadvantages. As such, while this article provides an interesting overview of how Rolls Royce verifies their cast parts, it should be read critically and taken with a grain of salt due to its lack of evidence and one-sided reporting.