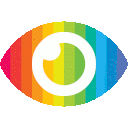
1. Shot peening is a widely used method to strengthen the surface of metal parts.
2. The effects of shot peening parameters such as velocity and coverage were analyzed using a random multi-shots model with dislocation density-based constitutive equations.
3. Increasing peening velocity can thicken the refining layer and compressive residual stress layer, while increasing coverage can heighten the magnitude of maximum compressive residual stress in subsurface. Double peening can induce larger surface compressive stress while reducing surface roughness slightly.
The article titled "Effects of different shot peening parameters on residual stress, surface roughness and cell size" published in ScienceDirect discusses the impact of various shot peening parameters on the surface integrity of metal parts. The study establishes a random multi-shots model that incorporates dislocation density-based constitutive equations to analyze the effects of peening velocity, coverage, and double peening on residual stress, surface roughness, and dislocation cell size.
The article provides valuable insights into the impact of different shot peening parameters on the surface integrity of metal parts. However, there are some potential biases and limitations in the study that need to be considered. Firstly, the study only focuses on analyzing the effects of three specific parameters (peening velocity, coverage, and double peening) while ignoring other important factors such as shot size and material. This limited scope may affect the generalizability of the findings.
Secondly, while the article claims that increasing peening velocity can significantly thicken refining layer and compressive residual stress layer (CRSL), it does not provide sufficient evidence to support this claim. The study also fails to explore counterarguments or alternative explanations for its findings.
Thirdly, although the article mentions that an appropriate double peening process can induce a larger surface compressive residual stress (SCRS) while reducing surface roughness slightly, it does not provide any information about possible risks associated with this process. This lack of information may lead readers to overlook potential safety concerns related to double peening.
Finally, there is some promotional content in the article that may bias readers towards certain products or services. For example, one section suggests that using an appropriate double peening process can improve surface integrity more effectively than simply pursuing improved peening velocity or enhanced coverage. This statement may be interpreted as promoting a specific product or service without providing sufficient evidence to support its claims.
In conclusion, while the article provides valuable insights into how different shot peening parameters affect surface integrity in metal parts, it has some potential biases and limitations that need to be considered. Readers should approach this study with caution and consider alternative explanations for its findings before drawing any conclusions or making decisions based on its recommendations.