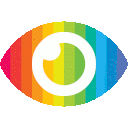
1. Laser powder bed fusion (L-PBF) is an additive manufacturing process that can create complex part shapes, but monitoring the process for consistency and performance can be challenging.
2. Property-based process monitoring using witness coupons is essential for L-PBF process validation and statistical quality control practices.
3. High throughput tensile (HTT) dogbones and bulk material bars can be used as witness coupons to detect shifts in the L-PBF process over time, providing valuable data for optimizing part performance.
The article "Long-term process stability in additive manufacturing" discusses the challenges associated with process qualification in laser powder bed fusion (L-PBF) additive manufacturing. The authors highlight the importance of monitoring properties such as microstructure, defect content, and surface quality to ensure consistent part performance. They also emphasize the need for statistical process control using witness coupons to detect shifts in the L-PBF process over time.
The study presents property-based process monitoring data from high throughput tensile (HTT) dogbones and bulk material bars. The authors demonstrate the sensitivity of small, high-throughput coupons based on their size and increased number of data points on each build. They establish paths to accurately identify sources of L-PBF process variability and compare the sensitivity of different ex-situ measurement techniques.
Overall, the article provides valuable insights into the importance of statistical process control for AM and highlights potential biases that can arise when selecting unsuitable witness coupons. However, there are some limitations to consider.
One limitation is that the study only focuses on one type of AM process (L-PBF) and one machine (ProX-DMP 200 from 3D systems). Therefore, it may not be representative of other AM processes or machines. Additionally, while the authors discuss the importance of monitoring properties such as microstructure and surface quality, they do not provide detailed information on how these properties were measured or analyzed.
Another limitation is that the study does not explore potential counterarguments or risks associated with using witness coupons for statistical process control. For example, witness coupons may not always accurately represent part performance due to differences in geometry or material properties.
Furthermore, while the authors discuss the benefits of using small featured, high-throughput samples for property-based monitoring, they do not address potential limitations such as reduced accuracy or precision compared to larger samples.
In conclusion, while this article provides valuable insights into statistical process control for AM using witness coupons, it is important to consider its limitations and potential biases when interpreting its findings. Further research is needed to fully understand the effectiveness and limitations of using witness coupons for AM process qualification.