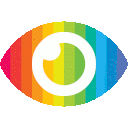
1. Composite repair systems using fibre-reinforced polymer (FRP) materials are being used as an alternative to traditional methods for repairing corroded pipelines in the oil and gas industry.
2. FRP repair systems have several advantages, including quicker application, elimination of fire and explosion risks, and cost-effectiveness compared to other repair methods.
3. The ASME PCC-2 and ISO 24817 codes provide guidelines for designing reliable and robust composite repairs, but there are discrepancies between the two codes in terms of defining certain parameters.
The article titled "Composite repair of pipelines, considering the effect of live pressure-analytical and numerical models with respect to ISO/TS 24817 and ASME PCC-2" discusses the use of fibre-reinforced polymer (FRP) matrix composite overwrap repair systems as an alternative method for repairing corroded or damaged pipelines in the oil and gas industry. The article highlights the advantages of FRP repair, such as its ease of application, ability to be performed while the pipeline is still in operation, elimination of fire and explosion risks, and cost-effectiveness compared to traditional repair methods.
The article mentions that more than 60% of oil and gas transmission pipelines worldwide are over 40 years old and in need of rehabilitation. It suggests that FRP repair can help restore these pipelines to their maximum operating capacity. However, it does not provide any evidence or data to support this claim. Additionally, it does not discuss any potential risks or limitations associated with FRP repair.
The article references ASME PCC-2 and ISO 24817 composite repair codes as guidelines for designing a reliable and robust repair. It presents an equation proposed by both codes for calculating the thickness of the composite repair based on factors such as internal pressure, pipe diameter, and material properties. The article then describes two different approaches used to assess the validity of this equation: analytical modeling and finite element analysis (FEA).
While the article provides some information about the strain in the composite repair laminate predicted by FEA at design pressure, it does not provide a comprehensive analysis or interpretation of these results. It only briefly mentions that the strain in the laminate exceeds allowable limits according to ASME/ISO standards in various situations but does not explore why this may be happening or discuss potential implications.
One potential bias in this article is its focus on promoting FRP repair as a superior alternative to traditional methods without adequately addressing potential drawbacks or limitations. The article also lacks a balanced discussion of the topic, as it does not present any counterarguments or alternative viewpoints.
Overall, this article provides some useful information about FRP repair of pipelines but lacks in-depth analysis and evidence to support its claims. It would benefit from a more comprehensive examination of the potential risks and limitations associated with FRP repair, as well as a balanced discussion of the topic.