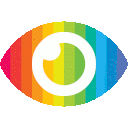
1. Fused deposition modeling (FDM) printed polymers have low mechanical properties compared to conventional composites, but there is a need for their recycling to reduce environmental pollution and manufacturing costs.
2. This study explores the use of FDM printed PLA as a core material in sandwich composites, with glass fiber reinforced polymer (GFRP) skins, to improve bending and shear performance.
3. The study found that the optimized resin uptake range in the skin/core interphase led to significant improvements in in-plane shear strength/modulus, out-of-plane shear strength/modulus, and specific peak bending load compared to the lowest performance sandwich composite. The 3D-printed cores were also found to have a satisfactory strength-to-weight ratio compared to balsa core sandwich composites.
The article titled "Bending and shear improvements in 3D-printed core sandwich composites through modification of resin uptake in the skin/core interphase region" discusses the use of fused deposition modeling (FDM) printed polymers as a structural material in composite structures. The authors highlight the need for recycling materials, such as FDM, to reduce environmental pollution and manufacturing costs. They investigate how the amount of resin uptake in the skin and skin/core interphase affects the bending and shear performance of sandwich composites.
One potential bias in this article is that it focuses solely on the benefits and improvements of using FDM printed polymers as core materials in sandwich composites. While the authors mention that FDM printed polymers have lower mechanical properties compared to conventional composites, they do not thoroughly explore or discuss the limitations and challenges associated with using FDM printed polymers. This one-sided reporting may give readers an incomplete understanding of the topic.
Additionally, there are unsupported claims made throughout the article. For example, the authors claim that their new manufacturing routine improves the incorporation of FDM printed polymers in composite structures without providing sufficient evidence or data to support this claim. The lack of empirical evidence weakens the credibility of their findings.
Furthermore, there are missing points of consideration in this article. The authors do not discuss potential risks or drawbacks associated with using FDM printed polymers as core materials, such as issues related to long-term durability, fire resistance, or regulatory compliance. These considerations are important for evaluating the feasibility and practicality of implementing this technology.
The article also lacks exploration of counterarguments or alternative approaches to achieving similar improvements in composite structures. By not presenting alternative viewpoints or discussing other methods for enhancing bending and shear performance, readers may be left with a limited perspective on the topic.
It is worth noting that there is no promotional content evident in this article. The authors focus on presenting their research findings rather than promoting a specific product or company.
In conclusion, the article provides some insights into the potential improvements in bending and shear performance of 3D-printed core sandwich composites. However, it has several limitations, including potential biases, unsupported claims, missing points of consideration, and unexplored counterarguments. Readers should approach the findings with caution and seek additional research to gain a comprehensive understanding of the topic.